Supply Chain & Manufacturing solutions
- Ruby Vision
- Nov 9, 2020
- 5 min read
Updated: Sep 15, 2022
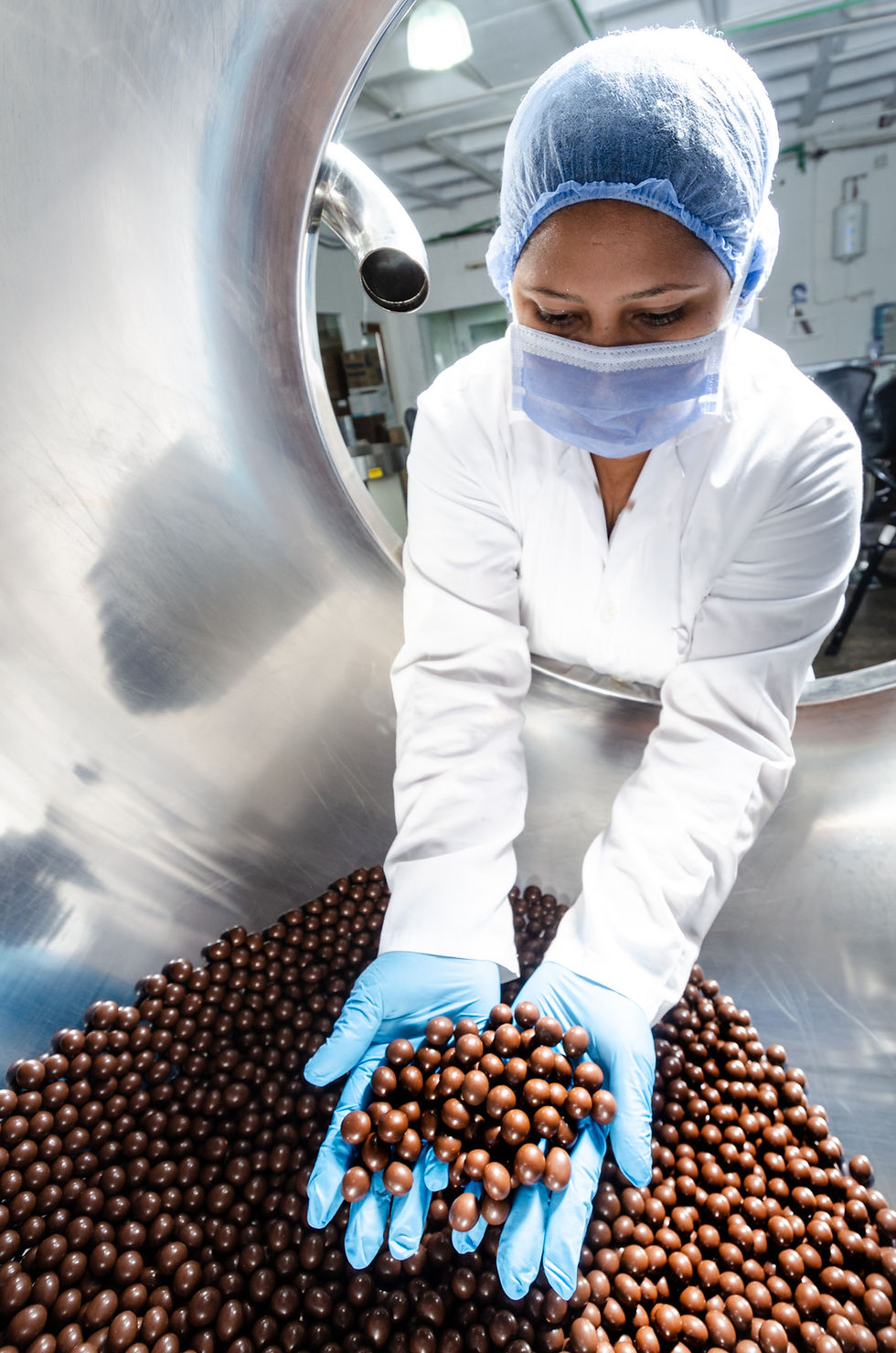
Introduction
RubyVision offers an integrated solution for supply chain management from brief through to invoicing. This offers a great advantage and significantly reduces integration costs and boosts productivity. For instance customer records are already present in the system as part of the CRM/Project interactions and the formulations are ready to be manufactured as they have been developed as part NPD initiatives. Supply chain becomes a smooth process giving you full control end to end.
Supply chain involves stocking to the right levels to maximise customer satisfactions and quicker turn around times. RubyVision offers powerful tools to analyse your material requirements and shortages with integrated auto re-order levels or checking raw material availability and shortages for orders on hand or forecasts/projections.
RubyVision is project/role based, so it offers a highly collaborated environment for various roles such as QC, purchasing, customer support, order fulfilment, logistics, etc to be upto date on order status or procurement. Automated email notification and dedicated Active views keeps everyone upto date on the work progress. Management get integrated reports to stay on top of their business.
Audit trials or history of every transaction is stored in the system. History of changes of sales order, purchase orders etc are also stored in the system. Recall reports are readily available that traces every batch that comes in or goes out of the system.
Material Planning & MRP
This is a complex area as material planing is based on
Past consumption
Product projections
Orders on hand
Past consumption & Auto Re-order levels
The system allows you plan materials from different perspectives so you can cross check and make the decision on the quantity to stock.
MRP
RubyVision has a powerful MRP tool that is integrated into sales orders to auto check stock availability in a single click with detailed shortage reports. It can also tell you what quantity is possible to facilitate part shipment to keep customers going.
Purchasing process
Purchasing can search on immediate shortages and raise purchase orders after reviewing the reorder levels. Once materials are received, the GRN process involves creating purchase batches of the stock received. This triggers notification to QC of goods in Quarantine stores. On AC approval stock can be moved to regular stores for manufacturing. Purchase batches created are linked to purchase orders for traceability and also allows batches to get its costs from purchase orders. When purchase invoices are entered the actual costs if different from PO costs will automatically propagate to the purchased batches and the product batches they are used in.
Purchase orders can be emailed from within the system. Dedicated Items on Order view is available for stores or purchases to know what to expect in the coming days. Items on order also integrated in inventory search screen so re-orders are avoided.
Every purchase stores details of QC along with links to purchase orders, expiry dates, allergen info, etc.
Processing Customer Orders
Processing orders on time is critical for customer satisfaction. In the previous section, the support tools such as auto re-order level and MRP based on orders on hand and projections ensured optimum stock levels.
When a order is received it is entered in a sales order. A sales order captures details of an order by integrating customer default preferences, picking prices based on volume based price slabs, taxes, etc. Managers and other relevant personal may receive notification of new orders.
For any product order users can link existing/floor stock directly to sales order and ship OR manufacture the shortfall and ship.
You can confirm the order to the customers by emailing to customers from within the system. Optionally an order may also go through an approve process.
Fulfilment status of orders are auto tracked based on the quantity dispatched. In addition you can configure additional user defined order status.
‘Items on Order’ and ‘Active sale order’ dedicated menus make it easy to stay on top of the status of pending orders. Orders with linked batches and QC approved can be easily spotted and shipped.
Shipping & Invoicing
Shipping is the process of dispatch goods. A shipping record consists of the details batches dispatched and the packing used to dispatch them (Inner and outer packing are supported).
The shipping record also tracks the freight details, dispatch dates, etc so it facilitates the generation of shipping docs and packing lists.
Sales Invoices are generated from shipping docs. Sales reports can be either generated from shipping records or from sales invoices. When a shipping occurs the accounts can be auto notified to generate invoices. The invoice can be generated from RubyVision and exported to your accounting system or directly generated in you accounting package.
The shipping process deducts stock of the shipped products from inventory.
Manufacturing
RubyVision is a batch based system - i.e. every stock is tracked by its incoming or outgoing batch, hence provides complete traceability to stock and costs.
The Product batch
A product batch consists of a unique code along with sales order references, schedules, status, QC data, etc.
The product batch stores the details of of raw material or sub product batches and the quantities consumed by the batch. Editing raw material quantities adjusts inventory stock levels.
Once manufacturing is complete the QC tab allows the QC to store the results of QC data.
The Documentation tab allows you to generate batch sheets and labels for the product being manufactured.
Manufacturing options
When a product batch is scheduled it may be in any of the following state:
Un processed
Reserved
Manufactured
Un-Manufactured
Reserve Manufacturing
This is another powerful feature of the software that allows you reserve available stock for any order even when there are shortages. You may get in critical order but there is shortage for few raw materials. If you do not reserve existing stock then later, then other batches may take away available stock so reserve manufacturing ensures available stock are reserved.
In fact reserve manufacturing ensure accurate FIFO batch allocation logic. When a order comes in, reserve manufacture even if all stock is available and schedule the batch. On the day the batch is to be manufactured, actually manufacture (from reserve manufacture —> manufacture) the product to allocate the raw material batches. This ensure smooth batch allocation and FIFO compliance as consuming batches before manufacturing will cause incorrect batches to be locked in the system and violate FIFO.
Reserve manufacturing also offers the ability to unreserve one or more items for high priority orders.
Scheduling & Batch status
Further you can configure batch status. A batch status can be in any user defined status. Typical status values could be Scheduled, Physically manufactured, QC Approved, Rejected, etc.
When a batch is created in any of the state or status production, QC, logistics personal can be assigned and scheduled and notified. As each personal complete their tasks status changes for other personal to take over.
The Active product batch view allows production to view batches awaiting manufacture this week, this day, etc so work can be planned and executed. Meanwhile QC can view batches that are pending QC and record the QC results against specs and approve the batch for dispatch.
The List view can be configured to display the required fields such as planned manufacturing dates, planned dispatch dates, etc. Shortages are also integrated in the list view. All batches can also be searched in the regular product batch view. You can also filter on ‘Production groups’ that group product types based on the equipments allocated for various product types.
Other Manufacturing options
Warns usage of expired raw material batches
Warns presence of food allergens (Food manufacturers)
Allows for multiple formulations per product to handle manufacturing variances without loss of traceability
Tracks the exact formula costs for the batch based on the raw material batches used.
Tracks priority and cleaning methods
Supports QC re-validation records
Supports auto grouping & generation of manufacturing instructions for similar product types
Supports yield
Allows to group product types and schedule them.
Facilitates auto generation of manufacturing instructions at the formulation level for similar products types.
Inventory Management
You can check stock at a site, location or store level. When manufacturing within a location, stock is auto pulled from the stores configured from that location. Inventory items are purchased into stores as batches.
Every batch status is stored in the system and every transaction is stored in the inventory history table so audit trials are easy to obtain. You can easily adjust stock and move stock between stores.
Comments